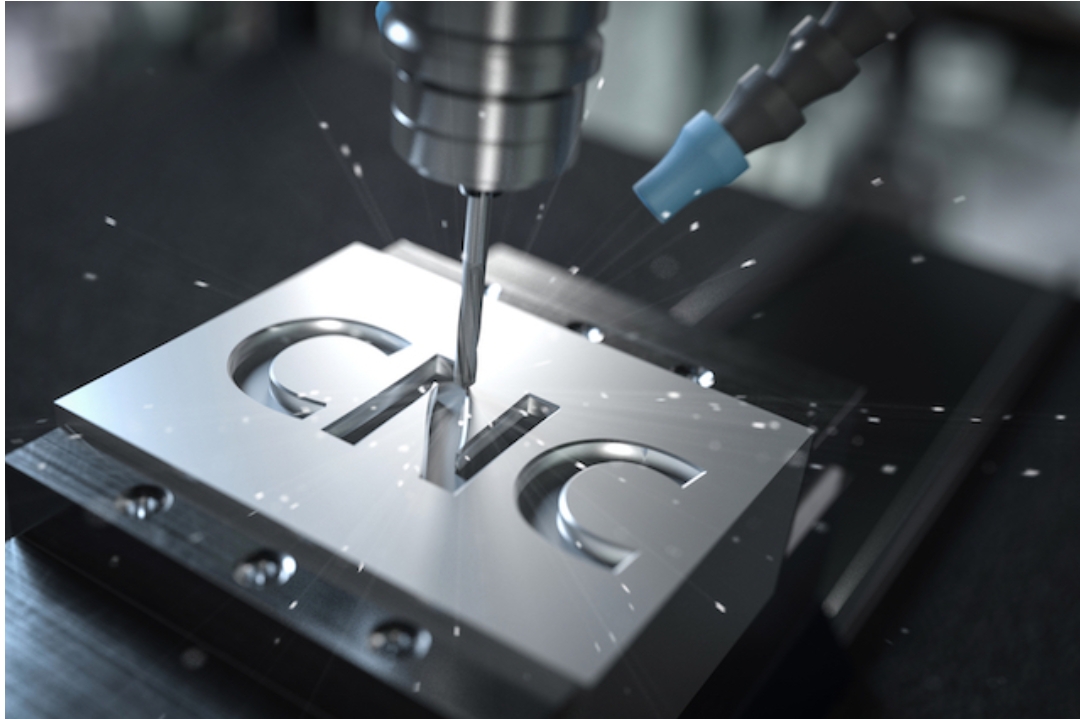
CNC Machining Innovations: How Technology Pushes the Boundaries of Precision
Over the past few decades, CNC machining has grown tremendously, becoming a base for industries needing high precision and efficiency. CNC Machining Technology is advancing at an ever-increasing rate, from medical devices to aerospace components, where its breadth is not bound.
These innovations are changing how parts are created, made, and distributed on intricate applications that demand small parts CNC. If you live for B2B, following the inbound and keeping up with the latest CNC machining trends for competitive advantage is important.
This guide finds new groundbreaking innovations in CNC machining and their impact on precision manufacturing.
Multiple Axes Machining
The multi-axis machining centers are one of the greatest accomplishments in CNC machining. Modern multi-axis machines can have three axes (X, Y, and Z), or they could have five or even seven. It also helps produce highly complex geometries in one setup, reducing the need for multiple machining operations.
For industries such as aerospace, multi-axis CNC machines can be beneficial because automotive components are sometimes extremely complicated, with many layers and extremely tight tolerances. These machines are perfect for small components CNC manufacturing, producing highly detailed parts with little error.
Multi-axis machining also improves production efficiency and increases consistency between batches with fewer setups. Leading precision engineering and CNC machining manufacturer investing in multi-axis technology means faster lead times and higher quality.
Integration of AI and Automation
Based on integration of artificial intelligence (AI) and automation, CNC machining has moved from considerable errors and lacking efficiency to a new level of efficiency and accuracy. With that, AI-powered systems can analyze complex designs, foresee machining issues, and optimize tool paths for the best possible results. On the one hand, however, automation is carried out to minimize human intervention, decrease errors, and increase production speed.
These technologies are especially helpful for B2B companies in scaling operations without losing quality. In this example, a CNC machining manufacturer takes advantage of AI-driven systems that can quickly adjust to design changes, so the production of custom parts will not encounter any hiccups. At the same time, automated systems can do repetitive work so the skilled operators can devote themselves to more complex parts of the production.
AI and automation are big game changers for small parts CNC manufacturing. For industries such as medical devices and electronics, they guarantee that even the tiniest components are produced with uniform precision.
Additive and Hybrid Manufacturing
Today, CNC machining has invariably been subtractive (removing material to make parts), yet integrating additive manufacturing techniques has offered possibilities. Additive manufacturing, or 3D printing, is building parts by printing successive layers of new materials and fusing them. Hybrid manufacturing fuses subtractive and additive processes to produce very complex parts that are impossible to machine with traditional means of manufacturing.
Combining precision machining and design complexity makes hybrid manufacturing attractive for many intricate and custom parts. For example, a base structure could be built with additive CNC machining techniques. The side components, the CNC machining consumables, would be achieved through subtractive CNC machining for exact tolerances.
This approach is especially appealing for prototyping and low-volume production as it reduces material waste and lead times. Hybrid manufacturing is a good way for B2B businesses to keep down costs while at the same time producing innovative products.
Real-Time Monitoring and IoT
The net application of the Internet of Things in CNC machining systems is changing how manufacturers monitor and market out-of-door production methods. CNC machines made IoT-enabled have sensors that feed in real-time data of parameters like Temperature, Vibrations, and Tool wear. Once analyzed, this data is used to optimize machine performance and maintain the same quality.
Real-time monitoring has benefits for B2B firms. This allows manufacturers to identify subsequent problems before requiring unnecessary downtime or creating defective parts. And IoT systems can offer valuable insights into how production efficiency can be improved for a business.
IoT-enabled machines bring high-quality standards to every small part of CNC manufacturing. For industries such as automotive and aerospace, a level of precision this high is crucial, as very small defects can mean big problems.
Advances in Cutting Tools and Materials
Advances in advanced cutting tools and materials have also contributed to the development of CNC machining. Modern high-speed cutting tools have been developed to survive higher temperature peaks for longer tool life and thus can run at faster machining speeds and higher accuracy. The paper also pointed out that materials like carbide and ceramic have increasingly become staples in the industry and provide higher performance than traditional steel instruments.
It is vital to choose the cutting tools for small parts CNC. Advanced tools are available for manufacturers to produce fine details and smooth finish, even in the most complex geometries. Moreover, high-performance cutting tools minimize tool changeovers and increase overall efficiency.
Those CNC machining manufacturers that keep pace with these advancements can provide their customers with great results at lower prices. Partnering with manufacturers that invest in state-of-the-art tools means that B2B businesses gain access to parts that meet the needs of today’s industries.
The manufacturing landscape is being transformed by CNC machine innovations that help B2B companies achieve new precision, efficiency & flexibility levels. From advanced multi-axis machining to the integration of AI, IoT, and hybrid manufacturing, these technologies are driving the limits of what CNC machining can provide.
Thanks to the advancements in these ways, small-part CNC manufacturing in industries that need small parts ensures they are made with full accuracy, even to the smallest of small parts. B2B companies can maintain their competitive edge and introduce dynamic solutions to customers by forging partnerships with leading CNC machining manufacturers.
Up next in relevant development, CNC machining has virtually endless potential as the technology advances. CNC machining innovations are making their mark on the future of precision manufacturing. Whether improving production efficiency, reducing costs, or enabling breakthrough designs, that future is just starting. It’s not an option; it’s a requirement for B2B companies to embrace these advancements to stay competitive.