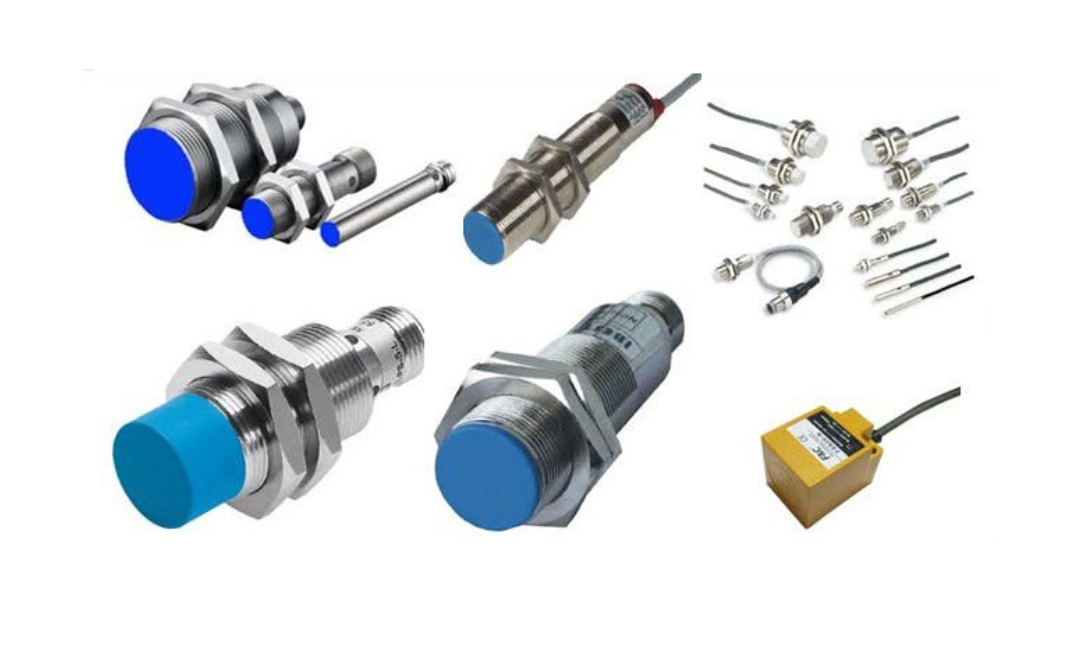
Maximizing Performance with Proximity Sensors in Automated Lines
Proximity sensors are an important element of the contemporary automated lines, providing accurate contactless detection in numerous industrial applications. These increase productivity, guarantee safety, and offer stable operation under numerous complicated automation procedures. This paper reveals a guide to classification of Proximity Sensors and utilization to distributors and manufacturers of industrial automation to boost their manufacturing lines.
In this guide, the author discusses the high-performance achievement of proximity sensors and explains why industrial facilities cannot do without these devices.
The Role of Proximity Sensors in Automation
Proximity sensors are important elements of the automated lines, allowing applications where an object within the definition range does not come into contact with the sensing part. These types of sensors are crucial in the sense that they quantify the existence, non-existence, or proximity of an object in a system, which is important in controlling the machinery, monitoring processes, and safety.
This is because proximity sensors of automated lines provide increased accuracy as compared to manned ones. For example, such sensors are often used in assembly lines to track the position of their parts to avoid distortions in positioning. Manufacturers who buy products from industrial automation distributors are frequently advised to use proximity sensors as one of the best solutions to improve the manufacturing process.
Types of Proximity Sensors
It is vital to distinguish between the types of proximity sensors to utilize to optimize the automation of what you want. Every sort of sensor has its own characteristics and some distinct uses to perform different operations. The most common types include:
1. Inductive Proximity Sensors
Intended especially for detecting metals, inductive sensors are very sturdy and thus suitable for use in applications with extreme working conditions. They find extensive usage in automated systems for identifying objects like the elements of a machine or metals.
2. Capacitive Proximity Sensors
These sensors are capable of sensing other metals as well as non-metals, including plastics, liquids, and timber. They have a general purpose and are applied wherever the materials being measured differ.
3. Photoelectric Proximity Sensors
As compared to an optical switch, the photoelectric sensor uses light for the identification of objects, is characterized by a longer range, and is excellent for the identification of small and transparent objects. They are also very common in packing industries and in industries with a production line.
4. Ultrasonic Proximity Sensors
Ultrasonic sensors utilize sound waves by which objects are detected and are best suited for distance measurements. They are finding use, especially in automation systems that are characterized by such features as high accuracy and long-range targets.
Knowing these types of proximity sensors gives an organization insight into choosing the types of sensors to use in their automated lines.
Enhancing Performance in Automated Lines
With the usage of proximity sensors, the speed of operations, accuracy, and reliability of the lines are improved. Here are a few ways they maximize efficiency:
- Precision Detection: The mechanism of operating the proximity sensors is accurate and can be repeated, thus making failures in the automated methods invariable. The following accuracy reduces errors so as to increase productivity.
- Non-Contact Operation: Proximity sensors do not require direct contact with the object of measurement and, therefore, do not cause additional wear and tear of materials, leading to their early deterioration.
- High-Speed Performance: Automated lines need quick responses, and the use of proximity sensors in detecting objects within a millisecond range is ideal for maintaining high-speed line performance.
- Flexibility: As there are many possibilities for proximity sensors, companies can adjust their automation systems depending on the nature of the application, whether the application is for detecting metals, liquids, or non-metallic materials.
These benefits are among the reasons industrial automation distributors provide when recommending proximity sensors for modern integrated manufacturing systems.
Benefits of Proximity Sensors for B2B Automation
As applied to the lines whose functional organization relates to B2B businesses, proximity sensors bring a number of advantages. Some of these benefits include:
- Cost Savings: The longevity achievable with proximity sensors also affects maintainability, hence reducing the long-term costs of using them in businesses.
- Safety: That is why proximity sensors are widely used in safety applications to help employees avoid the violation of safety regulations while working in dangerous areas.
- Energy Efficiency: Proximity sensors assist in energy conservation, a concept incorporated in manufacturing green technologies since it affords fine control of the otherwise automatic systems.
- Scalability: Some proximity sensors can be installed into the existing automation system that exists in businesses, hence the scale of the business, without necessarily having to overhaul the systems.
These benefits make proximity sensors an important tool for companies that seek ways to improve their automated lines.
Choosing the Right Proximity Sensors
Choose wisely the kind of proximity sensors to install within your industrial environment since their functions may vary depending on the type. They come in an array of shapes and sizes that are described as follows:
The problem of choosing proper proximity sensors is crucial for reaching high-efficiency goals for automated lines. Businesses should consider the following factors:
1. Application Requirements
Some of the important factors to consider when choosing a type of sensor include identifying the type of objects to be detected and the surroundings and conditions of the sensors. For example, inductive sensors are well suited for metal detection, but capacitive sensors are well suited for non-metal objects.
2. Detection Range
When selecting the sensors, avoid using those that will pick signals that are too close or those that are far from the source. The ultrasonic counter specifies long-range non-contact detection and the photoelectric counter specifies long-range operation, the inductive counter specifies short-range operation.
3. Durability
These are especially desirable in extreme temperature settings, high dust, humidity, and excess vibration typical in some industrial applications.
4. Compatibility
The sensors should also work with the already existing automation systems and the interfaces in the same way. There is also the option to contact trustworthy distributors of industrial automation products who can give necessary recommendations on which sensors will be the most suitable for a specific application.
Proximity sensors are highly rated components in enhancing the performance of automated lines since they provide precision, reliability, and versatility in the industrial fields. Due to the different forms of proximity sensors, organizational automation systems can be made more appropriate to the desired needs to enable faster and more efficient processes.
Conclusion
This paper, therefore, concludes that by engaging in close communication with industrial automation distributors and, in so doing, sourcing sensors from reputable manufacturers, businesses can realize the benefits of proximity sensors.
From identifying metallic objects through the use of inductive sensors to determining distances through the use of ultrasonic sensors, the appropriate proximity sensors can greatly enhance automation processes and speed up and enhance the safety and reliability of the sequence.
Recent advances in proximity sensor technology offer significant benefits to those manufacturing firms seeking improved competitive advantage: it is simply good business.